In the automotive sector, innovation is not just focused on electric drivetrains or self-driving features of the car. It also includes the ideation, the design, as well as the manufacturing parts. Stellantis, an automotive company which owns brands such as Jeep, Ram, Peugeot, Chrysler, Fiat and Maserati, is one of the companies which is on the track for this innovation header.
Besides releasing new cars into the market, Stellantis has also grabbed the attention with virtual reality (VR) headsets, 3D printing, and other technologies used for modern car manufacturing. Instead of being dreams of the future, these technologies serve real purposes in Stellantis’s design and production lines. Let’s now jump into the why and how questions we have about why Stellantis is using these technologies and their impacts on the automotive world.
The Change to Digital Car Manufacturing
The traditionally designed cars require a lot of time to be manufactured. The entire process is laborious, involving numerous prototypes, rigorous tests, logistics coordination, and so much more. Sketching concepts, building models in clay, and real-world crash tests would all be completed in the traditional car-making cycle.
But many automobile companies, including Stellantis, are now adopting a more tech-driven approach where most of the frameworks have shifted to the digital world. In this new world, tools like VR headsets and 3D printers can take over traditional methods.
Considering the revolutionary development of virtual tools, engineers, designers, and production teams do not have to wait until a part is manufactured. They can fully immerse themselves in reality-sized 3D models. Stellantis is making new decisions in the newest stages of vehicle development with the help of this technology.
1. Virtual Prototyping
Forget about spending resources and time on creating clay or metal prototypes. With the help of animation systems, Vagabond Stellaris, designers can step into a model and inspect it from every angle and evaluate its ergonomics. Additionally, they can work with their colleagues remotely, making real-time changes. This acceleration allows for streamlined decisions to be made during early-spent cycles, resulting in the expenses of remote collaborations being streamlined, the overall “cost” of collaboration between different countries from different countries all around the world.
2. Cross-Team Collaboration
With Stellantis engineers or designers located worldwide, it is only a flight of hours away. Virtual reality enables collaborative work. Whether it is a designer in Italy or a VR engineer in Michigan, real-time edit stimulation apply.
3. Simulated Manufacturing & Assembly
Stellantis leverages VR technology to simulate the assembly line visualization. Engineers and workers examine whether processes for installing parts are seamless and if there are any accessibility concerns. This minimizes occupational mistakes, enhances ergonomic effectiveness, and averts expensive redesigns post-assembly.
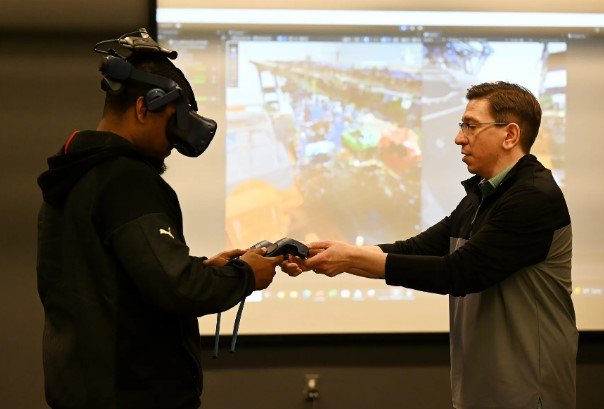
3D Printing: The Physical Counterpart to VR
While Stellantis uses VR to envision and make refinements, 3D printing transforms theoretical concepts into tangible objects within hours. The company employs additive manufacturing during various stages of the automobile’s life cycle, from design and prototyping to production.
1. Rapid Prototyping
Stellantis’s engineers can print precision small parts, jigs, and even vehicle-scale models, which can now be put through physical testing. For example:
New aerodynamic side mirrors can be evaluated by printing and testing.
Ergonomic assembly line worker-specific sculpted tools can be custom printed.
2. On-Demand Manufacturing
In limited production runs or with concept vehicles, Stellantis sometimes manufactures parts on demand, which streamlines inventory management.
3. Sustainability and Waste Management
3D printing technology offers clear advantages over traditional subtractive manufacturing methods, as it requires markedly lower inputs, resulting in far less waste. Stellantis is leveraging these benefits to simultaneously achieve sustainability goals and decrease material and energy consumption.
Stellantis’s Advantages from These Technologies
The operational and strategic advantages for Stellantis with the adoption of VR and 3D printing are profound:
1. Accelerated Time-to-Market
Advanced features enable shorter design and testing cycles, allowing vehicles to move from concept to dealership more quickly—this agility serves as a major competitive advantage in rapidly shifting industry landscapes.
2. Reduction in Costs
Streamlining physical prototype creation significantly decreases associated costs, along with tooling and production rework expenses, resulting in multi-million dollar savings per vehicle program.
3. Innovation and Personalization
The adoption of such technologies enables Stellantis to offer enhanced customization and more audacious experimental designs, which is crucial in response to a growing consumer demand for personalized vehicles.
4. Enhanced Quality and Safety Measures
Stellantis is able to enhance build quality and safety by addressing design or manufacturing oversights using virtual simulations and rapid prototyping during the preliminary stages.
Looking Closely at Stellantis’ Innovations
One of the most noteworthy ones is the use of Stellantis’ Virtual Engineering Integration, which uses integrated VR and digital twin technologies for visualization of full-blown cars and testing scenarios. This technology was extensively used during the brand-specific electric model development for Jeep and Peugeot.
In another example, a Stellantis plant in Italy used 3D printing technologies for ergonomic assembly line tools to make the assembly line more comfortable for workers, reducing the risk. These ergonomic technologies not only benefit the vehicles but also the veritable builders.
Stellantis: AI, AR, And The Future
Alongside transforming workflows at Stellantis with VR and 3D printing, the company also looks to the future. AI is being integrated for automating tasks like design generation, quality control, and predictive maintenance to increase operational efficiency.
Furthermore, AR is being applied for real-time digital assembly instructions for parts projecting onto the actual parts for augmented assembly, aiding visual instruction. This innovation will create further efficiencies while reducing errors.
Applying 3D printing and VR headsets as Stellantis does illustrates the integration of technology into the workplace strategically. In contrast, striving for sustainability with such advancements in technology reflects changing consumer expectations and the coming race for electric vehicles and autonomous driving changes automated thinking for manufacturers.
Stellantis is showing how traditional industries can transform by incorporating digital technology into the design process and utilizing swift manufacturing processes. In many respects, it is no longer simply the vehicles that are changing; the processes in which automobiles are produced are also shifting.
If Stellantis maintains this rate of innovation, prepare for further pioneering changes in the production of your next vehicle, well before it ever touches the pavement.